انواع خوردگی؛ خوردگی گالوانیک
خوردگی گالوانیک (خوردگی فلزات ناهمسان که به اشتباه الکترولیز نامیده میشود)؛ یکی از مهمترین انواع خوردگی است.
این نوع از انواع خوردگی، به تخریب دو ماده متفاوت در یک الکترولیت و محیط خورنده اشاره دارد. این اتفاق زمانی رخ میدهد که دو (یا چند) فلز متفاوت در زیر آب تماس الکتریکی داشته باشند.
زمانی که یک ترکیب گالوانیک (دوفلزی) تشکیل میشود، فلزی که سریعتر دچار خوردگی میشود آند است. و فلزی که در برابر خوردگی مقاومتر است کاتد نام دارد.

هنگامی که تماس با یک فلز متفاوت ایجاد میشود، نرخ خوردگی هر دو فلز تغییر میکند. در خوردگی گالوانیک، خوردگی فلز آند، سریع تر و خوردگی فلز کاتد، کندتر متوقف میشود.
اتصال گالوانیک مبنای بسیاری از تکنیکهای پایش خوردگی است. نیروی محرک خوردگی، تفاوت در اختلاف پتانسیل دو فلز است.
تاریخچه اتصالات گالوانیک
نیروی محرکه دوفلزی در اواخر قرن هجدهم توسط لوئیجی گالوانی در طی یک سری آزمایشات، کشف شد. در این آزمایشات ماهیچهها و اعصاب یک قورباغه در معرض یک رسانای دو فلزی قرار میگرفت و منقبض میشد. بعدها الساندرو ولتا که اولین سل الکتریکی (یا باتری) را در سال 1800 ساخت به صورت عملی از این اصل استفاده نمود.
تعدادی از دو نوع دیسک فلزی، توسط دیسکهای مقوایی آغشته به محلول اسید یا نمک جدا شدند. این مسئله که پایه و اساس گسترش باتریهای مدرن شد، یک کشف علمی فوق العاده به حساب میآمد. زیرا این روش به عنوان اولین متد برای ایجاد جریان الکتریکی پایدار شناخته میشود.
این اصل در راستای محافظت از سازههای فلزی در اوایل قرن نوزدهم طراحی شد.پ همفری دیوی (Humphry Davy) و مایکل فارادی (Michael Faraday) طراحان اصلی این طرح بودند. خوردگی فلزاتی مانند روی، منیزیم یا آلومینیوم یک روش گسترده برای حفاظت کاتدی سازههای فلزی است. در ادامه با تعداد دیگری از انواع خوردگی، آشنا خواهید شد.
در انواع خوردگی چه اتفاقی رخ می دهد؛ خوردگی گالوانیک
حال میخواهیم بدانیم خوردگی گالوانیک چه تفاوتی با دیگر انواع خوردگی دارد، و همچنین در این نوع خوردگی چه اتفاقی رخ میدهد.
در یک ترکیب دو فلزی، مواد فعالتر تبدیل به آند سل خوردگی میشوند. همچنین تمایل به خوردگی با سرعت بیشتری نسبت به زمانی که تنها هستند و با چیزی ترکیب نشدند دارند. مواد نجیبتر به عنوان کاتد در سل خوردگی عمل میکنند.
خوردگی گالوانیک میتواند یکی از رایجترین انواع خوردگی و همچنین یکی از مخربترین آنها باشد.
با اندازهگیری پتانسیل خوردگی یک ماده میتوان میزان نجیب بودن نسبی آن را پیش بینی کرد. به منظور تخمین اختلاف پتانسیل بین دوفلز، سری EMF طراحی شده است.
کوچک بودن نسبت آند به کاتد یک اتفاق ناخوشایند است. زیرا در این حالت، جریان گالوانیک بر روی یک ناحیه کوچک آندی متمرکز میشود.
در این شرایط، آند سریعتر ضخامت خود را از دست میدهد. سلهای خوردگی گالوانیک را میتوان در سطح ماکروسکوپی یا میکروسکوپی ایجاد کرد. در سطح ریزساختاری، فازهای مختلف یا سایر ویژگیهای ریزساختاری میتوانند در معرض جریانهای گالوانیکی قرار گیرند.
انواع خوردگی؛ خوردگی شیاری
خوردگی شیاری از انواع خوردگی موضعی است. خوردگی شیاری را میتوان در شیارها یا سطوح محافظت شده که محلول راکد وجود دارد، پیدا کرد. این یکی از رایجترین و در عین حال مضرترین انواع خوردگی موضعی است. زیرا در آلیاژهایی مانند فولاد ضد زنگ اتفاق میافتد که معمولاً مقاومت کاملی به خوردگی نشان میدهند.
خوردگی شیاری در مناطقی رخ میدهد که بلافاصله قابل مشاهده یا در دسترس نیستند. بنابراین خوردگی شیاری ممکن است منجر به خرابی ناگهانی فلز در وسیله شود.
شیارها یک محیط شیمیایی ایجاد میکنند که عملکرد متفاوتی از سطوح آزاد دارند. این اتفاق، روند خوردگی را سریعتر میکند. این محیط، رطوبت را حفظ و آلایندهها را جذب میکند، همچنین محصولات خوردگی را تغلیظ و اکسیژن را حذف میکند.
در بیشتر موارد، خوردگی شیاری در محلولهای نزدیک به خنثی رخ میدهد. در آن اکسیژن محلول، واکنش دهنده کاتد است.
عواملی که ممکن است به وسیله آن ها شیارهایی برای وقوع انواع خوردگی ایجاد شود
1) هندسه ساختار
- صفحات پرچ شده
- سازه جوش داده شده
- اتصالات رزوه شده
2) تماس فلز با مواد جامد غیر فلزی
- پلاستیک
- لاستیک
- شیشه
3) رسوبات ماسه
خاک یا محصولات خوردگی نفوذپذیر بر روی سطح فلز (نوعی از انواع خوردگی شیاری که به عنوان حمله رسوب نامیده میشود).
4) اجزای واکنش دهنده از حالت انرژی بالاتر به حالت پایین تر میروند
در خوردگی خشک، فلز و اکسیژن با هم ترکیب میشوند و اکسید روی سطح را تولید میکنند. این واکنش منجر به ترکیب (اکسید) در سطح انرژی پایینتر میشود.
لایه اکسید، از فلز در برابر اکسیژن محافظت و مانع ایجاد میکند. اکسید با اکسیژن موجود در هوا یا فلز واکنش نشان نمیدهد. این مانع، تماس اکسیژن در هوا را با فلز دشوار میکند. در نهایت آنقدر ضخیم میشود که حرکت الکترونها و یونها در سراسر آن متوقف میشود.
در صورتی که لایه اکسید ترک ایجاد نکند یا برداشته نشود، فلز در برابر خوردگی مقاومتر خواهد بود.
مکانیزم مدل Fontana، انواع خوردگی شیاری را توصیف میکند. این مدل شامل چهار مرحله است.
مکانیزم Fontana که انواع خوردگی شیاری را توصیف میکند، شامل مراحل زیر میشود:
یونهای فلزی دارای بار مثبت با –OH تعادل الکترواستاتیک دارند.
- در این مرحله، واکنش کاتدی داخل شیار، بیشتر اکسیژن موجود را مصرف میکند.
- –Cl و –OH در شیار پخش میشوند تا حداقل انرژی آزاد نشده را حفظ کنند و کلرید فلز تشکیل میشود.
هیدرولیز کلرید فلز باعث کاهش pH و میشود.
- یونهای
بیشتر به –Cl جذب میشوند. این امر منجر به کاهش pH داخل شیار میشود. انحلال فلز سریعتر شده و یونهای
بیشتری تولید میشود که منجر به کاهش pH خواهد شد.
شکل زیر مکانیزم انواع خوردگی فعال و غیرفعال و واکنشهای آندی و کاتدی مربوط به آن را در خوردگی شیاری نشان میدهد.

انواع خوردگی؛ ترک خوردگی تنشی ((SCC) Stress Corrosion Cracking)
یکی دیگر از انواع خوردگی، ترک خوردگی تنشی (SCC)، یک شکست در آلیاژ در معرض محیط است. که به دلیل یک کشش نسبتا کم اما ثابت رخ میدهد. یک عمل هم افزایی از محیط خورنده و تنش کششی بر روی مواد لازم است تا SCC ایجاد شود.
شکل زیر سه عامل مورد نیاز برای ایجاد SCC که یکی از انواع خوردگی است را نشان میدهد.

هنگامی که فولادهای زنگ نزن با محیط مرطوب در تماس هستند، لایه پاسیو شامل اکسید کروم است که هیدراته شده (Sedriks 1986). نرخ خوردگی یکنواخت فولاد زنگ نزن در این صورت به علت تشکیل فیلم پاسیو بسیار کم خواهد بود.
با این حال، لایه پاسیو ممکن است به صورت محلی در نقاطی که لایه پاسیو تضعیف شده وجود داشته باشد. مثل آخالها، رسوبها و مرزدانهها یا نقاطی از محلول که به علت تجمع یونهای متهاجم جدایش رخ داده است، اتفاق بیفتد. به عنوان مثال یون کلرید در زبری سطح تجمع میکند و باعث شکست لایه پاسیو میشود.
شکست لایه پاسیو
این شکست محلی لایه پاسیو منجر به ایجاد انواع خوردگی موضعی میشود. مثلا خوردگی حفرها و ترک خوردگی تنشی.
به دلیل تفاوت در ترکیب شیمیایی فولادهای ضد زنگ، ترکیب لایه پاسیو برای انواع مختلف فولادهای ضد زنگ نیز تغییر میکند. با این حال، کروم همچنان بخش بزرگی از لایه پاسیو را تشکیل میدهد که باعث محافظت از لایه سطحی میشود.
شرایط کار در یک دوره زمانی ممکن است باعث ایجاد بستری برای وقوع ترک خوردگی تنشی (SCC) شود. بنابراین، اکنون دیدگاهی مورد توجه قرار گرفته است که بیان میکند برای ایجاد ترک خوردگی تنشی (SCC) ترکیب محیطی خاصی ضروری نیست.
تنش کششی مورد نیاز برای ترک خوردگی تنشی (SCC) میتواند کمتر از تنش محصول ماکروسکوپی باشد. با این حال، تنشهای باقیمانده به دلیل فشارهای جوشکاری/حرارتی و فشار های بالا میتوانند منجر به ایجاد ترک خوردگی تنشی (SCC) شوند.
این اتفاق، در صورتی که فشار حاصل از مقاومت آلیاژ به صورت موضعی در مواد فراتر رود امکان پذیر است. انواع خوردگی SCC میتواند ترک خوردگی تنش بین دانهای ((IGSCC)intergranular stress corrosion cracking)، یا ترک خوردگی تنش میان دانهای ((TGSCC) Transgranular stress corrosion cracking) باشد. یا حالت ترکیبی از هر دو را به نمایش بگذارد.
پیشرفتهای چشمگیری در زمینه ترک خوردگی تنشی فولادهای ضد زنگ در دو دهه گذشته حاصل شده است. به ویژه درک مهندسی مرز دانه و کارکرد ساختار که بر ترک خوردگی تنش تأثیر میگذارد.
انواع خوردگی؛ خوردگی CO2
از خوردگی CO2 میتوان به عنوان یکی از مهم ترین انواع خوردگی اشاره کرد. دی اکسید کربن (CO2) در میدانهای نفت و گاز در غلظتهای مختلف یافت میشود.
از انواع خوردگی CO2 ،CO2 خشک، در مرحله گاز یا سیال فوق بحرانی، باعث خوردگی فلزات و آلیاژها نمیشود. با این حال، در حضور مایعات تولید شده حاوی آب، امکان خوردگی شدید زیرساختها به دلیل تشکیل اسید کربنیک وجود دارد.
عوامل موثر در خوردگی CO2
- غلظت CO2 (و اجزای دیگر مانند H2S)
- شیمی آب
- شرایط عملیاتی
- نوع مواد
انواع خوردگی CO2؛ خوردگی در صنعت نفت و گاز
مدتهاست که تاثیر اقتصادی خوردگی CO2 برای صنعت نفت و گاز شناخته شده است. برای کاهش اثر از روشهای بسیاری استفاده شده است. با این حال، با توجه به افزایش شیوههای جدید با افزایش دما، فشارها و ترکیبات سیال تولید شده متفاوت، عملکرد خوردگی مواد مجدد باید ارزیابی شود.
خوردگی CO2 به عنوان یک مشکل رایج در زمینههای تولید نفت و گاز به حساب میآید.
تجزیه، تحلیل و استخراج مدلها
با وجود به تلاشهای سیستماتیک برای تجزیه و تحلیل و استخراج مدلهای مناسب برای پیشبینی این نوع از انواع خوردگی، هنوز همه جنبههای آن مشخص نیست و در مورد مکانیزم و پارامترهای موثر بر آن نیز ابهام وجود دارد.
علاوه بر این، مدلهای اطلاعاتی موجود و دقیق، در مورد محیطهای دارای خوردگی شدید جزئیاتی ندارند.
کربن دی اکسید خشک؛ انواع خوردگی CO2
کربن دی اکسید خشک در دمای معمول سیستمهای نفت و گاز خورنده نیست. اما پس از حل شدن در فاز آبی، باعث واکنش الکتروشیمیایی بین فولاد و محیط میشود.
مایعات هیدروکربن؛ انواع خوردگی CO2
گاز CO2 حلالیت بسیار بالایی در آب و آب شور دارد و حلالیت آن در هیدروکربنها کمی بیشتر است.
مایعات هیدروکربن به طور کلی در تماس با فاز آبی تولید میشوند. همچنین در بسیاری از موارد، مخازن هیدروکربن حاوی مقدار قابل توجهی CO2 هستند. در نتیجه، CO2 در فاز آبی محصول هیدروکربن حل میشود و این فاز آبی باعث خوردگی فولاد کربنی خواهد شد.
مکانیزم های خوردگی CO2
مکانیزمهای خوردگی دی اکسید کربن پیچیده هستند. در ابتدا، گاز CO2 در آب حل میشود تا یونهای بی کربنات، اسید کربنیک و یونهای هیدروژن تولید شود. این اجزا توانایی حرکت به سمت سطوح فلزی و کمک به واکنش کاهش را دارند.
واکنشها از جمله بی کربناتها منجر به افزایش نرخ خوردگی، بالاتر از آنچه که از میزان اسیدیته انتظار میرود، میشود. در دمای کمتر از 60 درجه سانتیگراد و مقادیر pH، کمتر از 4، خوردگی با میزان تولید یون آهن با سطحی پوشیده از کربنات آهن کنترل میشود.
در بسیاری از موارد، پوسته نیمه محافظ کربنات آهن در دماهای بالاتر از 70 درجه سانتی گراد تشکیل و واکنش به صورت کاتدی کنترل میشود. این اتفاق سرعت خوردگی را کاهش میدهد.
این میزان همچنین با فشار جزئی CO2، دما و pH (کنترل غلظت یونهای بی کربنات) و شرایط سیال کنترل میشود. بیشترین میزان خوردگی در حدود 70 درجه سانتی گراد گزارش شده است. (کرمانی و مرشد، 2003؛ اشمیت، 2015)
برخی دیگر از مکانیزمهای مختلف برای این نوع از انواع خوردگی پیشنهاد شده است. همه آنها شامل اسید کربنیک یا یون بیکربنات هستند که از حل شدن CO2 در آب تشکیل میشود. این میزان، خوردگی بالاتری را نسبت به آنچه که در اسیدهای قوی در pH مشابه انتظار می رود، ایجاد میکند.
با حل شدن CO2 در آب، اسید کربنیک ایجاد میشود که در مقایسه با اسیدهای معدنی ضعیفتر است. (نیبورگ، 2002 ؛ گلدان ، 1995)
مراحل واکنش اسید کربنیک به شرح زیر است. (کرمانی و مرشد ، 2003 ؛ اشمیت ، 2015 ؛ گلدان ، 1995):
مکانیزم معرفی شده توسط De Waard نیز به خوبی شناخته شده است. (de Waard et al.، 1991؛ de Waard، 1993؛ George et al.، 2004).
در رابطه با مکانیزم خوردگی CO2، بحثی در مورد زمان وجود سایر اجزای محلول در واکنش خوردگی وجود دارد. میزان خوردگی به فشار جزئی CO2 بستگی دارد. زیرا این پارامتر، تعیین کننده pH و غلظت اجزای محلول است.
در واقع، کل زنجیره واکنشهای الکتروشیمیایی، پیچیدهتر از موارد ذکر شده است. بسته به اینکه کدام مرحله میزان خوردگی را کنترل میکند، وابستگی واکنشهای خوردگی به pH و CO2 محلول متفاوت خواهد بود. (نیبورگ ، 2002 ؛ Pots ، 1995).
انواع خوردگی؛ خوردگی موضعی ناشی از CO2
در انواع خوردگی؛خوردگی موضعی ناشی از CO2 (خوردگی شیرین) یک نگرانی جدی در رابطه با خطوط لوله نفت و گاز است. بسته به وضعیت راکد بودن/جریان داشن و سرعت سیال، خوردگی موضعی CO2 به سه گروه شامل حفره، حمله mesa و خوردگی موضعی ناشی از جریان تقسیم میشود.
حفره در سرعت کم سیال و در محدوده دمای نقطه رخ میدهد. با افزایش دما و فشار جزئی CO2 حساسیت نسبت به ایجاد حفره افزایش مییابد. (اشمیت ، 2015 ؛ اشمیت و فاینن ، 2000 ؛ اشمیت و انگلس ، 1998).
انواع خوردگی؛ خوردگی حمله Mesa
خوردگی حمله Mesa نوعی خوردگی شیرین است که در سرعتهای کم تا متوسط سیال رخ میدهد. جایی که پوسته تشکیل شده از کربنات آهن در این شرایط ناپایدار است و نمیتواند سیال را تحمل کند. (کرمانی، 1997).
خوردگی موضعی ناشی از جریان، حین حرکت سریع سیال در بالای نقطه بحرانی شروع میشود که از حفره یا حمله Mesa آغاز شده و با آشفتگی ناشی از حفرهها و پلها سرعت میگیرد.
اگر پوسته کربنات، غشای محافظ را تخریب و حذف کند، باعث ایجاد حرکات و تنشهای موضعی در طول آن میشود. پس از حذف، سرعت بالای پوسته سیال اجازه تشکیل مجدد غشاء را نمیدهد.
تردی هیدروژنی چیست؟
معمولا هیدروژن فقط به شکل اتم یا یون هیدروژن میتواند با فلزات ترکیب شود. بنابراین، هیدروژنی که به صورت گاز پراکنده است، فرم مولکولی دارد و توسط فلزات در دمای محیط جذب نمیشود.
با این حال، با افزایش دما، مولکولها تمایل به تجزیه اتمهای جداگانه دارند. این فرایند باعث میشود اتمها بتوانند در دمای خاصی با مواد ترکیب شوند. مثلا هنگام پالایش نفت یا عملیات حرارتی.در مواد مذاب، میزان جذب بالاتر اتمها مشاهده شده و این بدان معناست که فرایندهایی مانند ریختهگری و جوشکاری میتواند فرصتهای خاصی را برای ترکیب هیدروژن با مواد فلزی فراهم کند.
یونهای هیدروژن نیز توسط واکنشهای مرتبط با فرایندهایی مانند خوردگی، آبکاری و حفاظت کاتدی تولید میشوند. در نتیجه، فرصت زیادی برای ترکیب هیدروژن با اجزای فلزی وجود دارد. ترک خوردگیهای مرتبط با تردی هیدروژن بر اساس شرایطی که در آن رخ میدهد، انواع گوناگونی دارد که شامل موارد زیر میشود.
ترک سرد و ترک تاخیری
بخش دیگری از انواع خوردگی شامل ترک سرد و ترک تاخیری (ترک هیدروژنی) است. این بخش هنگام سرد شدن فلز و قطعات کار پس از جوشکاری فولادها ایجاد میشود.
_ ترک خوردگی ناشی از هیدروژن Hydrogen-induced Cracking (HIC) یا ترک خوردگی ناشی از فشار هیدروژن Hydrogen Pressure-induced Cracking (HPIC) :
جدا از معنای کلی آن، به مورفولوژی خاصی از ترک خوردگی در خطوط لوله فولادی و مخازن که باعث جذب هیدروژن میشوند، اشاره میکند.
– تنشی ناشی از هیدروژن Hydrogen-induced Stress Cracking (HISC) :
ترک خوردگی این نوع ترک خوردگی به ترک خوردگی هنگام سرویس در فولادهای داپلکس اطلاق میشود، ولی اخیرا رواج بیشتری یافته است.
انواع خوردگی؛ ترک خوردگی ناشی از عوامل محیطی Environmentally-Assisted Cracking (EAC)
این ترک خوردگی میتواند به دلیل تعامل بین اجزا و محیط اطراف رخ دهد و هیدروژن یکی از عوامل موثر بر این نوع ترک خوردگی است.
جدایش (Disbonding)
این اصطلاحات، مربوط به تکه تکه شدن کلد جوش داده شده مخازنی است که برای فرآورش گازهای هیدروژنی با درجه حرارت بالا استفاده میشود.
ترک خوردگی تنشی Stress Corrosion Cracking (SCC)
برخی از مکانیزمهای خاص این پدیده مربوط به تعامل با هیدروژن است.
ترک خوردگی تنشی سولفیدی Sulphide Stress Cracking (SSC)
خوردگی در محیطهای حاوی سولفید هیدروژن میتواند باعث جذب و ترک خوردگی هیدروژن شود. ساختار بلوری خاص فلزات نیز مهم است، زیرا بر سرعت انتشار و تغییر شکل هیدروژن تأثیر میگذارد.
بر این اساس، فولاد فریتیک نسبت به آلیاژهایی با ساختارهای کریستالی مختلف، مانند فولادهای زنگ نزن آستنیتی، آلیاژهای نیکل و آلیاژهای آلومینیوم، نسبت به شکنندگی هیدروژن حساستر هستند. با این حال، واضح است که هیدروژن میتواند باعث شکنندگی اکثر آلیاژهای مهندسی شود.
هنگامی که این اتفاق میافتد، شکنندگی هیدروژن میتواند باعث کاهش شکل پذیری و ظرفیت تحمل بار شود، که در نهایت منجر به ترک خوردگی و خرابهای شکننده خواهد شد.
انواع خوردگی؛ خوردگی کاویتاسیون
خوردگی کاویتاسیون یکی دیگر از انواع خوردگی است که با تشکیل حباب و ترکیدن آن در مایع رخ میدهد. خوردگی کاویتاسیون به عنوان فرسایش حبابی نیز شناخته میشود.
گرچه تفاوت نه چندان زیادی بین خوردگی کاویتاسیون و فرسایش حبابی وجود ندارد. درحین خوردگی کاویتاسیون، هم خوردگی و هم تخریب کاویتاسیون رخ میدهد ولی در حین فرسایش حبابی، فقط تخریب کاویتاسیون اتفاق میافتد.

خوردگی کاویتاسیون در تجهیزاتی مانند توربینهای هیدرولیکی، پرههای توربین، ملخهای هواپیماهایی که امکان فرود و حرکت در آب را دارند و پرههای پمپ رخ میدهد.

برای آشنایی بیشتر با این بخش در انواع خوردگی و درک شکلگیری و فروپاشی حفره در سیستم، استوانهای حاوی آب و مجهز به پیستونی محکم در نظر بگیرید. هنگامی که پیستون کشیده شود، حجم داخل سیلندر افزایش مییابد و در نتیجه فشار کم میشود. با کاهش فشار، آب شروع به جوشیدن میکند و باعث ایجاد حباب در دمای اتاق میشود.
هنگامی که پیستون به داخل حرکت میکند، حجم کاهش مییابد، فشار بیشتر میشود و در نهایت حبابها فرو میریزند.
این فرآیند بارها و با سرعت زیاد در توربینها، ملخها و پرهها تکرار شده و حین آن حبابها به سرعت تشکیل و بلافاصله از بین میروند. حبابهای در حال ترکیدن، باعث از بین رفتن لایههای محافظ روی سطح فلز میشوند.
سطح محافظت نشده فلز دچار خوردگی شده و مجدد تشکیل میشود. روند بازسازی و فروپاشی حباب، لایهای را که به تازگی روی سطح تشکیل شده از بین میبرد.
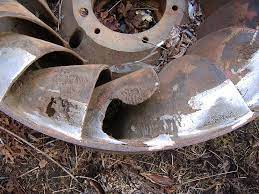
توصیف خوردگی کاویتاسیون
در نبود لایههای محافظ سطحی، تشکیل و از بین رفتن حبابها با تغییر شکل پلاستیک همراه است که باعث دور شدن ذرات فلز از سطح میشود.
خوردگی باعث گسترش کاویتاسیون میشود. بنابراین خوردگی کاویتاسیون یک فرآیند همافزایی شده است که شامل فرایندهای مکانیکی (تشکیل حباب و فروپاشی آن) و فرآیندهای الکتروشیمیایی است.
آسیب حفره را میتوان با به حداقل رساندن احتمال تشکیل حباب و فروپاشی آن کنترل کرد. این کار با طراحی سیستمهای هیدرودینامیکی با اختلاف فشار کمتر ممکن میشود.
در مورد پمپی که دچار کاویتاسیون میشود، روش استاندارد این است که فشار سیستم را به گونه موثری افزایش دهید، تا از ایجاد حباب در نقاط فشار پایین سیستم جلوگیری شود. به علاوه، سیستمهای هیدرودینامیکی باید از موادی ساخته شوند که در برابر خوردگی و آسیب مکانیکی مقاوم هستند.
با توجه به انتخاب مواد، باید توجه داشت که مواد شکلپذیر نسبت به مواد شکننده مقاومت بیشتری دارند. موادی که دیرتر دچار فرسودگی میشوند در برابر خوردگی کاویتاسیون نیز مقاومت بیشتری دارند.
با کاهش اندازه ذرات مواد، مقاومت در برابر خوردگی کاویتاسیون افزایش مییابد. سطوح ناهموار نسبت به سطوح صاف بستر مناسب تری برای ایجاد حباب فراهم میکنند.
سطوح مواد با پوششی محافظت میشوند که معمولا از جنس لاستیک یا پلاستیک است. در استفاده از پوشش، باید توجه داشت که اگر فاصلهای بین پوشش و فلز ایجاد شود، میتواند محل مناسبی برای بروز و ایجاد حفره باشد.
حفاظت کاتدی و استفاده از بازدارندهها و کنترل خوردگی، سرعت بروز خوردگی کاویتاسیون را کاهش میدهد. اما تاثیری در آسیبهایی که توسط نیروهای مکانیکی رخ میدهد ندارد.
خوردگی حفرهای
خوردگی حفرهای پدیدهای بسیار پیچیده است. با وجود مطالعات متعدد در زمینه انواع خوردگی طی قرن گذشته هنوز به طور کامل شفاف نشده است. با این حال، شرایطی که باعث شروع، گسترش وکند شدن روند خوردگی حفرهای میشود تا حدی شناخته شده است.
مکانیسم خوردگی حفره ای
چندین فرضیه سازگار برای توضیح مکانیزم خوردگی حفرهای ارائه شده است که مراحل اصلی آن در شکل زیر نشان داده شده است:

مکانیزم خوردگی حفرهای میتواند شامل مراحل زیر باشد:
1- شکست لایه پاسیو
2- توسعه حفره
3- پاسیواسیون مجدد حفره
این پارامترها اساساً به وضعیت لایه اکسید شده، ساختار فلز که ذرات بین فلزی در آن نقش عمدهای دارند، ماهیت محیط آبی اطراف و محتوای کلرید آن بستگی دارد.
نکته: خوردگی شیاری را میتوان به عنوان خوردگی حفرهای تفسیر کرد. اما تفاوت آنها این است که خوردگی شیاری در سطوح میانی محافظت شده در برابر مایعات رخ میدهد و امکان نفوذ اندک مایع وجود دارد. در حالی که خوردگی حفرهای، در سطوحی که با محیط مرطوب تماس مستقیم دارند رخ میدهد.
آغاز حفره
به گفته ریچاردسون، لایه اکسید شده دائما دچار تخریب و ترمیم میشود. که در محیطهای غیر تهاجمی، میتوان آن را فوراً ترمیم کرد. با این حال، در حضور محلول حاوی یونهای تهاجمی به ویژه کلریدها، دسترسی این آنیونها به سطحی مانع ترمیم آن میشود. سپس کنش پذیری لایه اکسید شده از بین میرود.
برای بسیاری از محققان، شروع حفرهها به دلیل نفوذ کلرید در لایه اکسیدی است؛ یا به این دلیل که آن لایهها دارای عیوب بیشماری هستند، که این عیوب تبدیل به نقاط ورودی کلریدها میشوند، یا چون در محلول آبی دارای بار مثبت میشوند.
این عیوب عموماً با ناهمگنیهای فیزیکی مانند وجود اجزاء و ذرات بین فلزی که لایه اکسید بر روی آنها نازک تر است، تغییرات فیزیکی سطح (به عنوان مثال خراش های ریز) ناشی از حرکات مکانیکی، صیقلدهی، تراش دادن سنگ یا عبور از ابزارهای شکل دهی مرتبط اند.
شروع ایجاد حفرهها یک پدیده بسیار سریع است و مشاهده آن دشوار است، زیرا در مقیاس یک میکرومتر اتفاق میافتد و علاوه بر این، ماهیت تصادفی دارد و نمیتوان مکان دقیق آن را پیش بینی کرد.
هیچ دوره نهفتگی برای شروع حفرهها وجود ندارد. وارنر و اشمیت توانستند زیر میکروسکوپ نیروی اتمی (AFM) روی آلیاژ AA2024 مشاهده کنند که تشکیل حفرهها در کمتر از 2 دقیقه در محلول کلرید سدیم رخ میداد. این میکروحفرهها با قطر 0.1 تا 1 میکرومتر، در تعداد بسیار زیاد با چگالی، شکل گرفته بودند.
شکست لایه پاسیو
چندین مدل برای توضیح شکست لایه پاسیو پیشنهاد شده است که شامل موارد زیر است:
- نفوذ آنیونها به لایه اکسید
- پارگی لایه اکسید
- جذب آنیونها توسط لایه اکسید
شکست لایه پاسیو، به یونها اجازه میدهد تا به فصل مشترک لایه اکسید/فلز برسند و در آنجا باعث انحلال فلز شوند.
دو توضیح برای نفوذ ارائه شده است:
وجود یک میدان الکتریکی بسیار قوی جذاب در لایه اکسید، که به ترتیب شامل 106 تا 107 V.cm−1 و بار مثبت در سطح لایه اکسیدی است.
به گفته مک کافرتی، برهم کنش با مولکولهای آب، لایهای از گروههای هیدروکسیل، +AlOH2 را در سطح فیلم اکسیدی با ضخامت 0.5 تا 0.8 نانومتر ایجاد میکند.
چگالی این گروههای هیدروکسیل بین 6 تا 20 نانومتر مربع است.
نقطه ایزوالکتریک لایه اکسید، روی آلومینیوم در pH 9.5 رخ میدهد. بنابراین، برای محلولهای خنثی با pH کمتر که با محیطهای طبیعی بیشتر مطابقت دارد، لایه اکسید دارای بار مثبت است و به طور طبیعی یونهای −Cl کلرید و آنیونهای دیگر مانند سولفاتها، −SO42 را جذب میکند.
شکست لایه اکسید به دلایلی مانند وجود جاهای خالی (Vacancies) در اکسید رخ میدهد. جاهای خالی با حرکت به سطح فلز/اکسید برای گرفتن کاتیون های +Al3 از فلز گسترش مییابند. اگر سهم این کاتیونها ناکافی باشد، آنها میتوانند حفرههایی ایجاد کنند،که به مکانهایی برای ایجاد حفره تبدیل خواهند شد.
برای اینکه آلومینیوم در سطح لایه اکسید/فلز حل شود، مولکولهای آب نیز باید بتوانند از طریق شکاف یا منافذ لایه اکسید به آن نفوذ کنند. این نواحی در اطراف ناهمگنی سطحی و حتی برش مکانیکی ناشی از حرکت، شکل دادن و صیقل دادن هستند.
نظریه برخی از محققان
جذب سطحی یک مدل است که در طول زمان مورد توجه بسیاری از نویسندگان بوده. Szklarska Smialowska معتقد است یونهای کلرید روی لایه اکسید جذب میشوند یا در هر دو ترکیب میشوند. کلریدها به دلیل اندازه کوچکشان به راحتی به لایهی اکسیدی نفوذ میکنند.
شعاع آنها 18.1 نانومتر است که کمی از لایه اکسیدی (14 نانومتر) بزرگتراند. حرکت آنها از طریق فضاهای خالی اکسیژن امکان پذیر است.
چندین روش تحقیق از جمله اتورادیوگرافی، جذب سطحی کلریدها را روی لایه اکسید نشان داده است. آستانه غلظت بحرانی کلرید مشخص نیست. با این حال، اگر چنین آستانهای وجود داشته باشد، غلظت کلرید باید حداقل باشد.
به گفته زید (Zaid) بین غلظت کلرید و پتانسیل حفره رابطه وجود دارد. اثر کلریدها با افزایش غلظت آنها کاهش می یابد. این ارتباط به ویژه بالای 1 درصد وزنی (%.1wt) بسیار واضح است.

در وب سایت رسمی شرکت نفتان پایش، در بخش مجله تخصصی خوردگی مطالب مرتبط با “انواع خوردگی” را خواهید یافت.
با ما همراه باشید.
منبع
https://www.nace.org/resources/general-resources/corrosion-basics/group-1/galvanic-corrosion
https://soar.wichita.edu/bitstream/handle/10057/917/grasp%20216.pdf
https://www.sciencedirect.com/topics/materials-science/pitting-corrosion
https://www.sciencedirect.com/topics/engineering/cavitation-corrosion
https://www.twi-global.com/technical-knowledge/faqs/what-is-hydrogen-embrittlement
https://www.sciencedirect.com/science/article/abs/pii/S1875510018303366